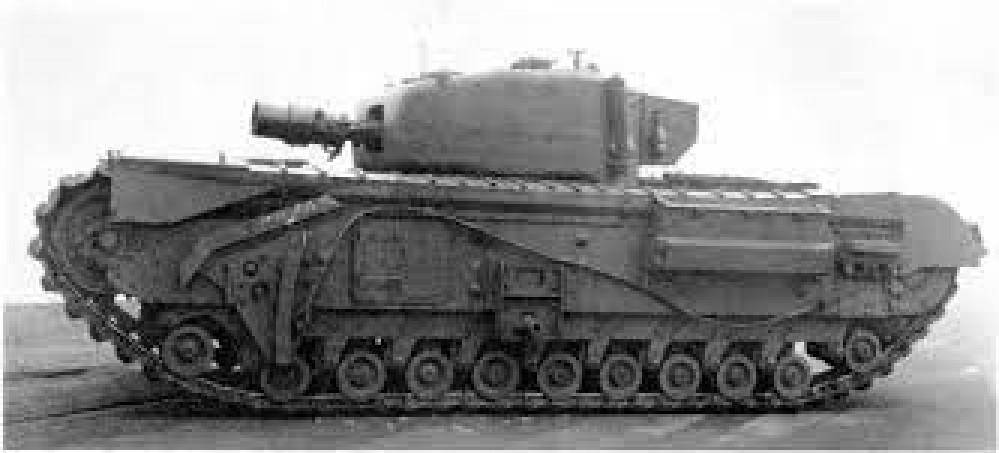
How to be an Armoured Farmer, building Hobart’s Funnies in Glorious 15mm (and maybe 28mm if they arrive in time!)
Recommendations: 2233
About the Project
Right then, having avoided any sort of Spring cleaning challenge in the past, I have decided to use this year's one to get something done that I have been gathering bits for over the past few years and finally finish and assemble all of my Hobart's Funnies. To get technical these are Armoured Vehicle Royal Engineers (AVRE) tanks, using the Churchill chassis as a base. I will also throw in some Sherman Crabs (Flail tanks). I have gathered a few books for reference so that I can paint and mark them up for one of the Armoured Assault Squadrons Royal Engineer (either 77, or 79) that landed ashore at Sword Beach and were the very first to see action on that beach; Plus the Sherman Crabs of A Squadron 22nd Dragoons. Whilst I want to be able to use the finished tanks in games depicting the D Day Landings (in Flames of War and Chain of Command at 15mm) I also want then to be versatile enough to be able to be used in later engagements that the 79th Armoured Division took part in (which is pretty much everything!). I hope you will find this of interest if you ever want to branch out into what the modern day Royal Engineers affectionately call being an armoured farmer.
Related Game: Flames of War: The World War II Miniatures Game
Related Company: Battlefront Miniatures
Related Genre: Historical
Related Contest: Spring Clean Hobby Challenge (Old)
This Project is Active
Which Airbrush to use
The first thing to say about airbrushes is that it is a very true statement that you get what you pay for. Having said that, if you are looking for something to basecoat with, then go for a cheaper single action brush. Single action means that the trigger doesn’t depress, that the air pressure is always there at the pressure set on the compressor regulator. When you pull back on the trigger more and more paint is allowed to flow into the airstream and out of the nozzle. Most single action brushes have a screw at the back so that you can set the maximum flow and thereby set the size of the line you are spraying. It is a good tool to learn on, you can get used to holding and handling the brush at the right distance and the use of the trigger in the best way.
Once learned, you can then move onto a double action airbrush and generate the muscle memory of applying downward pressure on the trigger to release greater pressure. You can still limit this by setting the maximum pressure on the compressor regulator.
I have inherited one of the airbrushes below. I found that Badger produce good quality brushes for a fair price and that will be a good starting point. I kicked off with a single action 200G and was then given a 200NH from my father-in-law, as he couldn’t get used to it. I totally understand, it is a bottom feed brush for large coverage jobs and I found it to be unwieldly and that it blocks up far easier than the top feed versions.
The next thing I would suggest is that when you buy a brush, get another needle/nozzle set at a larger size. That way when you get comfortable with a brush, if you want to do fine detail work, simply swap out the needle. I did this with the 200G and when using the fine needle I reduced the pressure to between 10-15psi.
My next purchase was a Sotar 20/20 with a 0.2 and 0.4 needle. This was bought after about 2yrs of practice on the 200G. I would say that when you move to 0.2 and below then it is critical that you thin your paint correctly and carry out regular cleaning throughout your paint session.
For my last birthday I was very fortunate to be able to afford a Harder & Steenbeck infinity CR plus. This is a very high quality airbrush and the difference it has made to my control and use has been tenfold. The higher quality leads to closer tolerances and finer machined parts which means that paint is less likely to adhere to them. I have found that as long as I thin the paints and clean it regularly then it paints amazingly. This brush came with 0.15 and 0.4 needles and I chose to use the 0.4 setup, as I was looking to base coat and then be able to go in and spray higher parts and central areas of large panels with a highlight colour.
Prep, prep and prep some more
Before you spray anything, make sure your area is clear of dust. I actually use my airbrush to blow the booth clear and then go over the bits to be painted. Next I apply any masking required, the best I have used is the Tamiya modellers tape, or the frog tape from any good DIY store. TOP TIP: if you find your tape is too tacky, stick it to your clothes (jeans are best) and then use it.
Next I mount everything I can onto some form of handle so that I don’t have to touch the model. It’s a bit of a faff but you get the benefits of not spraying too much on one area, or missing bits. The mounts are many and varied, including some very old GW paint pots (that still have paint in them).
Other bits to make life easier
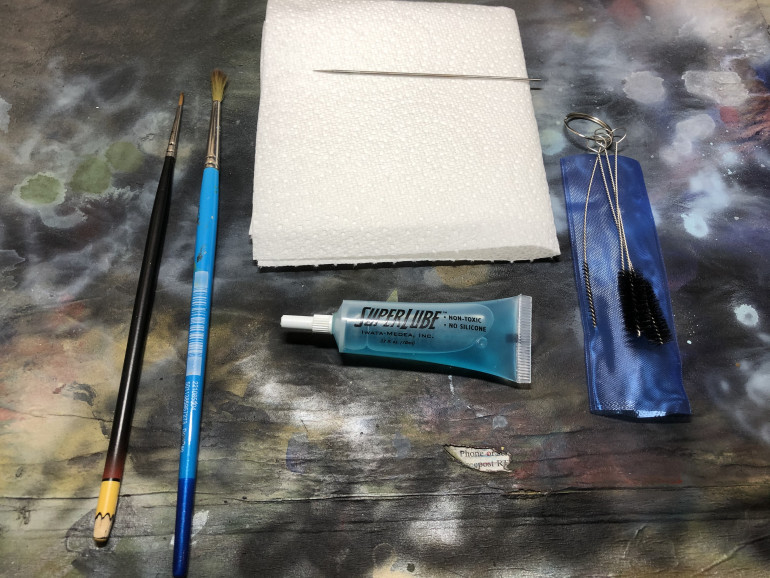
Essential bits and pieces
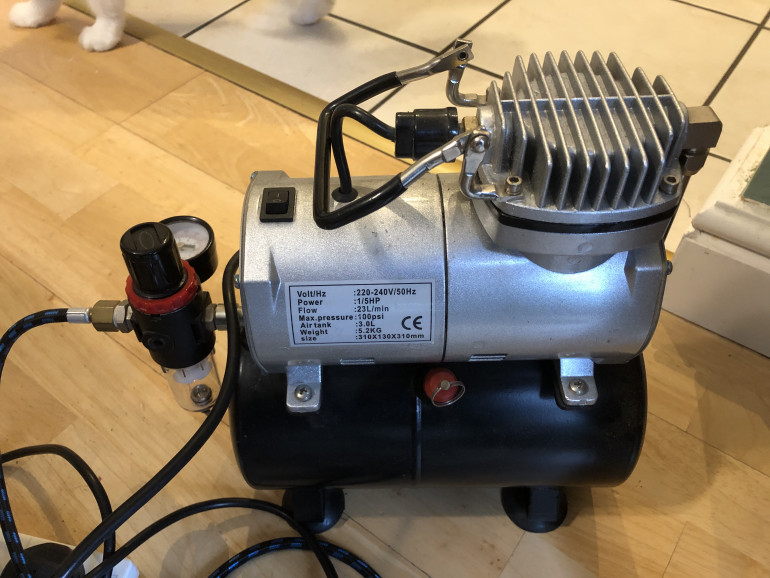
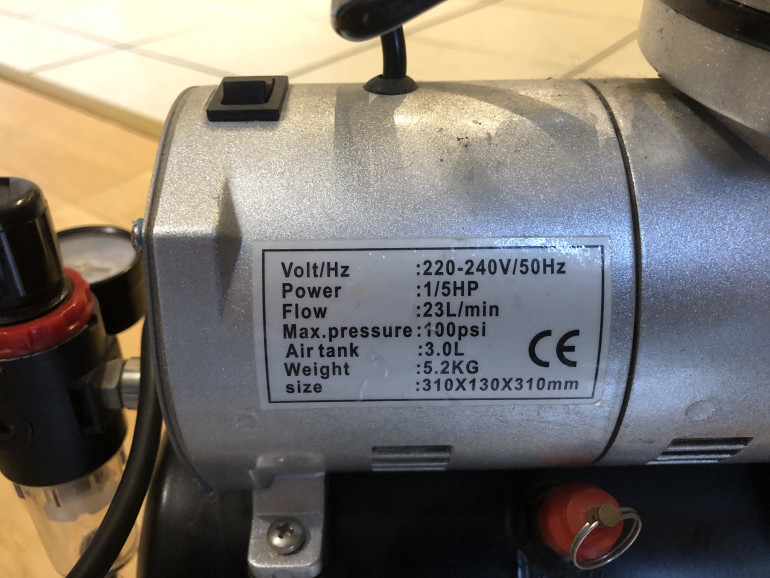
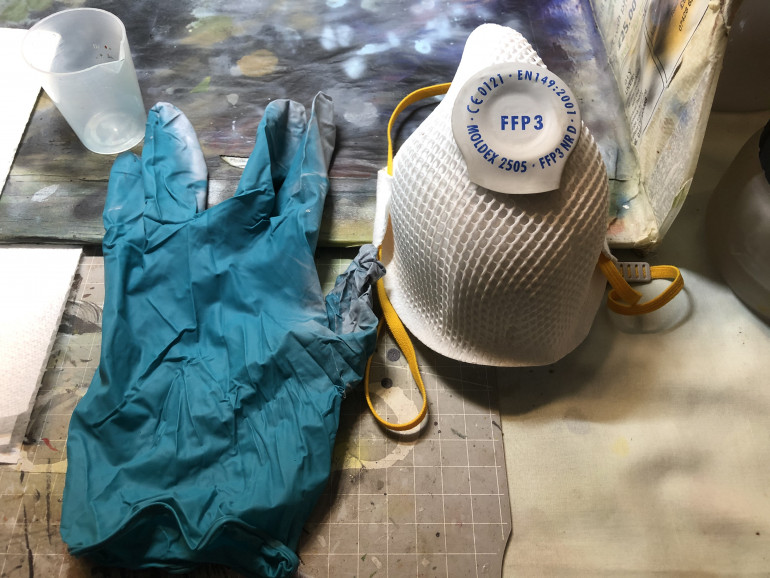
Time to apply paint
With everything built and all the gribblies added it was time to get some paint down. Now normally I’ll base coat with a rattle can but if there is a lot of fine detail I will airbrush it instead. I like to base coat tanks in black, so that I have instant shadows when I apply the colour. The colour in this case, for Late British WW2 tanks will be Vallejo Russian Uniform 70924. I use Vallejo base coats through my airbrushes but the one thing to note is that you do need to thin it down (I do 50/50 mix with Vallejo thinner). Whilst plastic models will take the Vallejo base coats really well, you must let any metal models dry/cure for at least 24hrs or there is a chance that it could peel back off.
The finished Builds
And here are the finished models, including a Lloyd shot!
The Porpoise
A strange name for a bit of kit but I can see why it was called such. This was a sled that is towed behind a tank (normally general purpose AVREs) and was water tight so would float until it reached shore and then be dragged behind the tank until jettisoned. The porpoise had hatches on top to give access to munitions and explosives that would be needed by Royal Engineers and infantry on the landing beaches.
I purchased two kits from S&S models and after cleaning them up I glued the fittings in place.
Also attached are a couple of drawings showing the design and the porpoise behind an AVRE.
AVRE Bobbin Conversion Cont'd
I then fed the completed carpet onto the Bobbin and left the front edge hanging down. I didn’t glue it in place yet, as I will paint the tank first, weather the carpet, before fixing it in place.
AVRE Bobbin Conversion Cont'd
To make the carpet I used some 1mm x 0,25mm styrene bar and wrapping paper. I cut the paper to size and then marked it up at 10mm intervals (leaving the first 30mm clear). I then glued 12 bars in place. Once dry, I folded the 30mm section over on itself so that this would become the free end of the roll.
AVRE Bobbin Conversion Cont'd
With all the parts created, I glued the brass axle in place, slid on the Bobbin, glued the support frame to the other end of the axle and then glued everything in place on the tank. The last bits were to glue the top beam in place and then add little pieces of brass rod to the bottom of the rear support arms so that they looked right.
AVRE Bobbin Conversion Cont'd
To add a bit of visual detail to the Bobbin roll, I marked up and glued supports to the circles. I used 1mm x .025mm rectangular bar for this.
AVRE Bobbin Conversion Cont'd
AVRE Bobbin Conversion Cont'd
After completing the main sections, I offered everything back up to the tank so that I could confirm the diameter of the ends of the Bobbin roll were going to fit.
AVRE Bobbin Conversion Cont'd
The next thing to create was the Bobbin roll itself. So that I didn’t have to make miles of carpet I decided to place an infill piece over the roll. After scaling the roll I found that a bit of 20mm plastic pipe would work brilliantly. After cutting the pipe to the correct lengths using a plumbers pipe cutter, I used the pipe as a former and cut a section out of the longer pipe section so that it would fit inside the other one. Once sanded smooth I superglued everything in place.
AVRE Bobbin Conversion Cont'd
Next up was the most fiddly bit, the front support arms. Each were made from two lengths of C channel (2mm x 1mm), and the infill pieces from 2mm x 1mm sections and 1mm square sections.
AVRE Bobbin Conversion Cont'd
First off I cut out the rear support arms, these were then drilled with a 1mm dia drill bit and the end rounded off. The other end will be cut off at an angle to match with the C Channel section of the front support arm.
AVRE Bobbin Conversion
With having the advantage of a 28mm version to scale off, I took measurements, sketched up the main support arms and then calculated the 15mm measurements from this information.