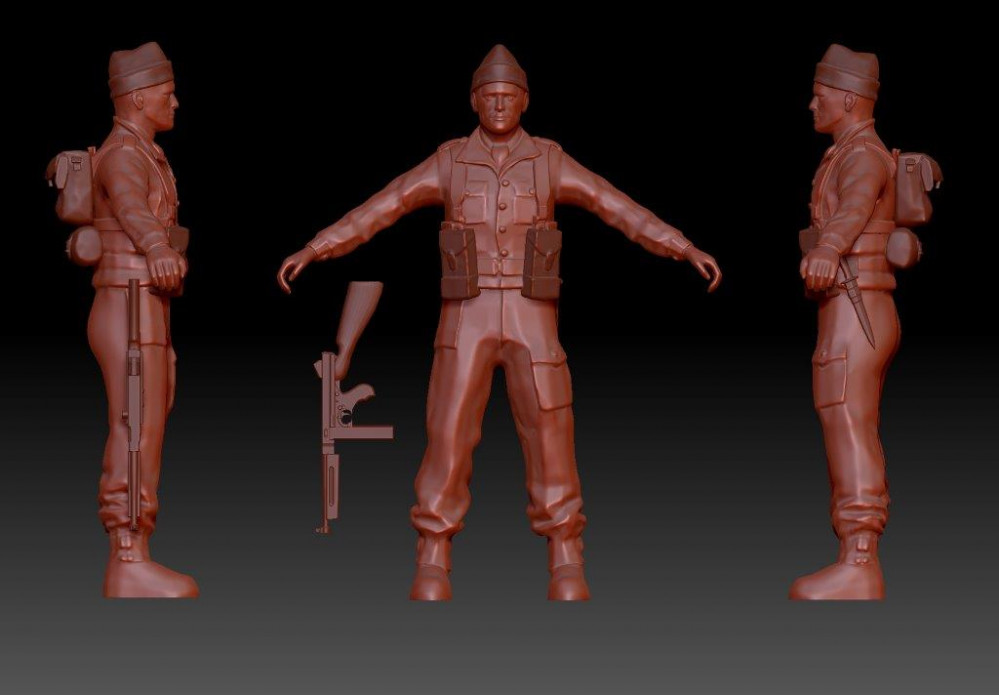
Spring Clean Challenge: Developing WWII infantry for 3D printing
Recommendations: 45
About the Project
After joining a forum conversation about the shortage of 3D printable WWII miniatures, I decided to have a go at creating my own.
Related Game: Flames of War: The World War II Miniatures Game
Related Genre: Historical
This Project is Active
Spring Clean Challenge
I’m blowing the dust off this project for my spring clean challenge.
It had been a while since I’d opened these digital files. In fact I had to read through this project to remind myself where I had left it!
In order to re-familiarise myself with Zbrush and create better models to work with, I decided to rebuild some of the components. I began with the Thompson which I reworked to a bulkier, more print friendly design.
I went back to one of the earlier soldier files and played around with his proportions. The figure on the left of the screen is the new model, with the original on the right. I’ve enlarged the head, hands and feet. I also bulked up his torso and arms and adjusted the proportions of his legs and hips. While I was at it I took the opportunity to bulk up details such as the collar and webbing. This was primarily to close up any holes that would cause problems in printing and make these details more pronounced.
Here you can see the new Commando model from the front and profiles, along with the bulked up Thompson to show its proportions.
Small Soldiers
The next step was to export the commando base from Zbrush as an OBJ file to be loaded into a slicer program (in this instance Preform). I decided to print another scale comparison so I made the first base of figures 6mm as well as a duplicate scaled to 8mm.
I positioned the first commando base in the slicer program and tried several different orientations in order to find the position that resulted in the fewest support struts being generated. As I had hoped, this turned out to be base down. This was ideal as it meant most of the supports would be beneath or against the base where they could more easily be removed.
I set the printer to the smallest layer size available (0.25mm), to get the cleanest print possible. Within a couple of hours I had the above prints out. The rafts protected the delicate models as I removed them from the print head to be cured. Interestingly the 6mm base required fewer supports, resulting in even less clean up. The 6mm also doesn’t seem to have lost any detail compared to the 8mm, although at such sizes it’s hard to tell for sure.
Unfortunately once again the 6mm figures broke at the ankle during handling. This kind of resin is hard and therefore brittle at such small sizes.
The 8mm faired a little better and I managed to snip away the supports without damaging the figures themselves. Hopefully you can make out some detail from these images. I have to say I’m pleasantly surprised by the results but the fragility of the figures is a bit of a problem. The guns have all printed this time although the barrels are pretty insubstantial on most of the figures. The Thompsons definitely need to be scaled up again, requiring a further increase in bulk. I think the easiest fix is probably just to inflate the whole model again, this time I’ll try 5% rather than 2%.
Squad Up
I decided to go back to my rigged model and have another go at posing. I was happier with the results this time and again went through the process of reintroducing details such as the packs and knife.
Again I swapped out the Thompson but this time I scaled it up by 10% and inflated it by 2% to give it a little more bulk and volume. I also increased the size of the head, hands and feet by 5% and finally inflated the whole model by 2%. The difference is subtle but I’m hoping all these changes will give me a little more bulk for printing.
This time I decided I would assemble a unit of models on a single base, to create a useable gaming piece. The only 6mm game I have played was Epic Scale 40k, back in the early 90’s (I think called the Horus Heresy at the time). The miniatures in this game were assembled on square bases of five marines, each making up half of a squad. Going with a similar convention I instead opted for a round base and made four clones of my Commando.
For the final version I intend to create five different poses but while I’m still running tests duplicates will do fine. I used the simple trick of mirroring two of the poses and positioned them at different angles to give a modicum of variation.
As a finishing touch I decided to add the British Commando insignia to the base!
Print Test II
Just a quick update on my second print test.
With the addition of a block beneath the miniatures they were strong enough to remove from the build plate. However this time they snapped at the ankle! On reflection this part of the model is less than a half millimetre thick on the 6mm figure. Positioned so closely to the base the ankle makes for a likely break point. You can probably also see from the attached images that the guns didn’t print successfully.
With these issues in mind I think I will have to make some concessions to the proportions of the model. This is something I had already considered but I wanted to stick as close to true scale as I could manage.
These figures really are very small but you can see details such as the back packs and even the knife on the hip have been retained. On my next test I will aim to reduce the number of supports as removing them on such a delicate model is tricky. It’s possible that a 6mm model is just too small to work with. The 8mm model seems to have been more successful, the extra volume giving it a little more robustness and detail.
Print Test I
My own 3D printer is due to arrive later this month but in the meantime I managed to run a test print on the printer we have at work (it’s also much better than the one I’ll be getting so a bonus really)!
I positioned my commando on his back with the SMG facing directly away from the build plate. This was in the hope that I could avoid the need for any support structure around the front of the miniature and especially the barrel of his gun. I reasoned the gun would be quite fragile and cutting away a support would likely result in snapping the barrel.
I left the print running over night and although it printed successfully the model was destroyed while being removed from the plate! The plastic used in SLA printing remains in a slightly jellyfied state until it’s cured under a solar lamp post printing. Unfortunately such a small component wasn’t strong enough to be removed from the print head successfully.
Lesson learned. This time I would print the model on a block to give it a little more integrity while it was being processed. I also decided I may as well print some size comparisons so I scaled a couple of duplicates up to 8mm and 10mm respectively.
Once again I arranged the component with its back to the build plate. This would mean the figures would be printed facing downwards, from back to front, as the build plate was raised from the resin bath below.
Eureka!
I didn’t see the point in taking a neutral pose forward as a test print so I figured I’d have another crack at posing. After a little homework I found out about a function callet Transpose Master. This operation drops the working model (referred to as a tool in Zbrush and often containing multiple sub tools), to a low polygon count in order to facilitate faster processing.
I also constructed a new rig as this was a process I could carry out pretty quickly now (10-15 mins). As soon as the new rig was bound to the soldier mesh I noticed big improvements. The lag I had suffered previously was now gone and the model moved freely. A further benefit of using Transpose Master was that I was able to bring the Thompson along with the model as a separate sub tool (I was only able to use a single sub tool with the previous rigging method).
I was able to create this pose in around 20 mins. It’s not perfect and you can see in the below images that some areas, especially the knife and Submachine Gun, have distorted very badly.
I had anticipated some clean up would be required to the posed model so I had replacement parts standing by. I swapped the Thompson and knife for undistorted versions from my earlier clean up and touched up the modelling here and there.
With the addition of a simple circular base my soldier was beginning to look a lot more like a gaming miniature.
Before exporting the model for printing I checked over the mesh. Specifically I needed to ensure that the model was ‘Water Tight’, which is to say that there were no holes into the mesh and no areas of hidden topology within the model. Once I was happy that the mesh was fit for printing I scaled him to a height of 6mm from the top of the base to the dent in his woollen hat. As I had conducted sculptural work on the model again the poly count had crept up to around 2 million so it was necessary to Decimate once more before exporting my Commando as an OBJ file.
Two Steps Back
I’ve hit a bit of a brick wall with this project.
I loaded my finished model onto my MKII rig and went through the earlier steps to pose him. Immediately I ran into problems. The model and rig suffered major slow down whenever I connected the two together. This made posing impossible as the rig moved out of sequence with my cursor or was completely unresponsive. After a frustrating hour of trying to resolve the problem I did the smart thing and consulted the internet.
What I discovered was that rigging with a model comprising circa 1 million polys (or points), is a fools errand. Who knew?! Certainly not me as there was no mention of this in the tutorials that had gotten me this far. My labours to improve my sculpt had resulted in an unwieldy amount of information which would have to be significantly reduced if I were to have any hope of posing it. Worse then, it seemed the low poly count of the original model was not the cause of the softening of detail after all. In my search for a solution to the lag problem I had noticed a slider that adjusted the resolution of the posed model.
Infuriating as this was my efforts had not been completely wasted. Zbrush has a tool for every task and I only needed to decimate my mesh to achieve a lower poly count. This could be done without loosing much detail as the function generates a more economical mesh, much like the original form of the model. To clarify, the higher density, evenly sized poly frame (Dynamesh), is necessary for modelling but is large and unwieldy in terms of sheer data. Now the modelling phase was complete, reverting to a lower density poly frame would result in a mesh that was easier to process and therefore manipulate.
Here are three key stages of the modelling process, each displaying their polyframes for comparison:
So now I had a re-sculpted, re-topologised model it was time to try rigging again. I took the Decimated mesh back to the rig and tried again. It moved a lot better and I was able to create the below pose, however I was still experiencing a lot of lag. One of the tutorials I watched mentioned a function that can be used alongside rigging and I think this is what I need to get my head around next. If I’ve understood correctly it allows you to pose a low resolution model (to get around the lag), then transfer that same pose to a much higher resolution version of the same model.
Again I must remind myself that the aim here is to produce miniatures as small as 6mm. I’m considering taking a break from modelling to progress a basic version of my model to the 3D printing stage. I think it’s worth seeing how one of these figures comes out.
Above all this project is about learning and I have learned a lot so far.
Going Commando
After finishing my clean up of the model I wanted to check it against some reference material. After a couple of searches on St Nazaire and British Commandos in general I pulled up some historical images. The first thing I noticed from photos taken at the time, was that the Commandos rarely seemed to have helmets on. Most of the images portrayed them in woollen beanie hats or berets.
This look was far more in keeping with the image of SSB troops that I had in my mind. I was tempted to go with berets but these seemed more for parade than operational use. In the end I modelled a woollen hat on my soldier using the reference images shown. It’s pretty basic but does the job of giving him a more elite appearance compared to the tin helmet worn by the infantryman.
I also played around with attaching the helmet to the pack. Although this wasn’t obvious from the images it offered me another detail option for the models.
My other concern was what weaponry would be appropriate as Rifles aren’t really in keeping with the mobile nature of commando raiding parties. The Wiki page for St Nazaire references that the men responsible for laying charges on key targets of the port would be armed with only pistols. They would be accompanied by units armed with Thomson or Browning Submachine guns who’s job it was to escort and cover them.
The compact nature of submachine guns would no doubt make life easier at the printing stage. Long, narrow rifle barrels would require support structures to print and were likely to snap when removing said support structure from the printed model.
My model only came with a rifle but the British Officer, available from the same supplier came with an M1A1 Thomson Submachine Gun, exactly what I needed.
I had intended to download this model at some point as it would give me the option of making a distinct Command unit. This is of course a staple for any Wargame.
Next stop Turbosquid.
The long way around
Going back to the figure in it’s original form, I took a look at the poly frame. As you can see in the image below the figure is made up of polygons of varying shapes and sizes.
This is not optimal for Zbrush modelling as the model behaves as though some areas are in higher definition than others.
There are several ways to even out the mesh and increase its density, improving the resolution of the model. The trick is retaining the detail while carrying out these operations. The simplest option was to subdivide the mesh, increasing the total number of polys. After a single subdivision the mesh looked like this:
As you can see the model is far less blocky but the details have begun to soften. Areas like the straps of the webbing, as well as buttons and buckles have begun to disappear.
At this point I am aware that on a 6mm model these details are hardly likely to be an issue. However things like this annoy me and I know with a little work I can achieve a better result. I’m enjoying working with this model and will probably continue to work with it beyond this project so I want to get the best out of it.
Opting to take the long way round I began separating the model into sections using the polygroups described earlier. By treating each element of the model individually I would be able to retain their form and even enhance some details, before bringing all the parts back together.
After a few hours work I was much happier with the new model. Below is a comparison of the face which has much greater definition than my first attempt.
MKII Rig
With my master model downloaded it was time for another lesson in rigging. I watched the tutorials again as I wasn’t quite sure how I’d gotten it to work the first time and knew I hadn’t followed each of the steps correctly.
I also wanted to create a neater and more anatomically correct rig. The tutorials elude to the need for an economy of design when building a rig/skeleton. Too few components and the mesh would stretch and distort around the internal framework. Too many and it would become infinitely pliable, bending all over the place and loosing any sense of anatomy.
The above image shows the new rig without the soldier mesh. The various protrusions around the spine are intended to ensure that the torso retains its volume as the model bends. I’ve put structure into the pack and webbing in an attempt to retain their form and position during posing.
After reposing the arms, tilting the head and improving the stance of the legs I ended up with this;
I found it beneficial to remove the helmet and reposition it manually after posing the figure, in order to retain its correct form.
I’m a little disappointed by the softening of the soldier’s form when I transfer the pose to the skin of the model. I suspect this is due to the topology of the mesh which was likely built for 3D graphics, rather than 3D printing . I think I need to do some work to the mesh prior to transferring it to my rig so I’m going back a step to revaluate.
Polygroups
Feeling confident that this process would work I decided to download the British Infantryman. For less than the price of a pint in your local London boozer I picked up this plucky chap.
Something I hadn’t thought to check on the previous model was whether it was made up of separate Polygroups. Switching the view mode on the new model I was happy to discover that it was divided into many different areas of topology. This is delineated by the different colours in this set of images.
Polygroups are, as one might expect, groups of polygons set to a common purpose. This essentially divides a model into sections that can be easily isolated. This is particularly useful for me here as I am able to remove entire parts of the model such as the helmet and pack, giving me more options not only in how the figure looks but in how I work with it.
First Steps
Once subdivided I made some changes to the figure’s pose by masking off sections of the body and moving them around. This is a very crude way of manipulating the figure and results in some messy areas of topology, particularly when making extreme adjustments. I had managed to pose the figure but I knew I could do better.
I had heard of the process of ‘rigging’ digital models to give them an internal skeleton. This would allow for more fluid movement and once achieved, would make for much easier manipulation of the figure poses. The free soldier I had downloaded came complete with an internal skeleton but it wasn’t something that could be used in Zbrush. I suspect it was designed for a program such as Maya but as I didn’t know (or have), that software, I would need to find an alternative solution. My next stop was YouTube to find some tutorials on Rigging in Zbrush.
After half hour of playing around while watching an excellent tutorial, I had made a basic rig.
More surprisingly, it actually seemed to work!
Testing the Water
As I wasn’t really sure if my plan to purchase a digital model and repose it would work, I thought it wise to test the water with a free download first. Fortunately a comparable model, a modern Russian Soldier, was available for free from the same designer.
Here is the free soldier after I downloaded and opened him in Zbrush (the program I will primarily be using). With a low polygon count he looks quite blocky but this could be improved by simply subdividing the geometry to give it more polys.
Concept
The thread that inspired this project was about Warrens St Nazaire game, as discussed on the weekender. The brief was to find a range of 3D printable miniatures to represent the British and German forces who took part in the conflict. While I am completely open to the idea that an alternative solution will be found, the parameters of this project have given me an opportunity to progress my digital learning, very much the focus of this year for me. In many ways this is about the journey, rather than the end destination.
After a brief internet search I found these 3D renders on Turbosquid.
They are fairly basic by today’s miniature standards but at $6 I would say they’re decent sculpts for the money. At time of writing the aim is to produce these figures in 6mm so nice simple shapes with low profile detail seems ideal.
They also come with separate rifles or SMG’s which will be handy for posing. The soldiers can also be purchased with ‘rigs’ for $10 (more on rigs later).