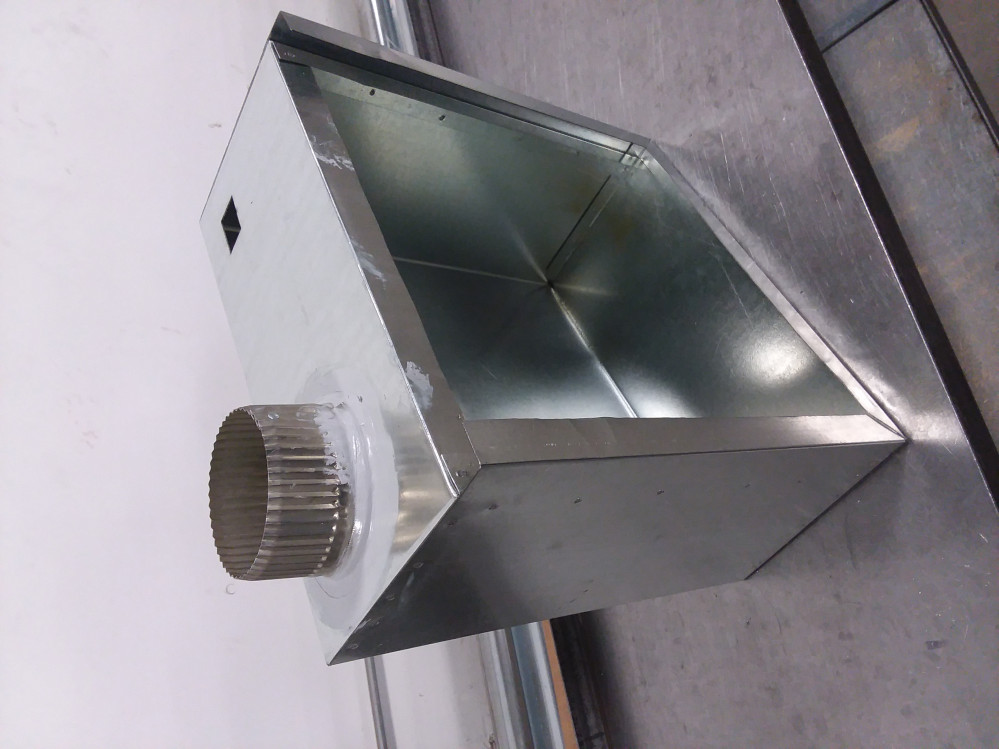
Venting my spleen… or atleast my airbrush
Recommendations: 62
About the Project
Building a better bespoke spray booth comparable to the BV300S-D. I've upgraded to the BV300S-D and will use this to aid in my apprenticeship and have it become a gift to one of my nephews as I mold him into a future nerd.
Related Genre: General
Related Contest: Spring Clean Hobby Challenge (Old)
This Project is On Hold
Only temporary setback
I’m mothballing this project out of realizing I am just not able to devote enough time to make it a reality. I bought a fully functional piece of equipment and I just don’t have need for the unit I planned on building. Perhaps I’ll take this up again in the future as I’m going deeper in study with sheet metal work. Maybe next year I can use it for my class project if I’m allowed opportunity to design one myself. Just tonight we started planning for fittings and the initial build process of parts. Its application of knowledge now and its a bit daunting even if I am in the shop. Here’s to a better tomorrow as I whittle down projects to better focus on completion.
Clearing the air
I’ve just gotten my Benchvent BV300S-D. I am excited as anything at the purchase. It also makes me excited to know my effort for my exhaust fan project has not been in vain. This quick look at the insides of the product should be a lesson for anyone else who wants to build something like it themselves.
It has a very swank outside to look at. On quick inspection the construction is very simple of a plain frame, sitting on a rubber gasket, that holds over the filter media with some hand tightened screws. This sits in front of the fan held inside the casing which pulls out the fumes. I thought it was going to be so much more difficult.
The only differences between what I’m doing thus far and this new unit for hobbying is that the Benchvent has a powder coat finish and what appear to be precision tack welds for the panels (which may very well be robotic but likely handmade).
Considering what I do in my shop all day with sheet metal I can do this myself no sweat. I could spend the money to coat my fan at a shop down the road but do I really need to? Nah, I’ll skip that and build up the fan without those bells and whistles.
Considering my current knowledge of electrical systems (i.e. none) I’ll turn to the Internet and learn. This might become what I do for my sheet metal apprenticeship course instead of some dumb toolbox project.
Back in the cabinet!
I’m back at work with ventilation again. Its been some time but the company I worked for previously that I was able to make the housing hired me a few months ago. I’m back to thinking about the fan build and I’ve looked at the EBM-Papst RadiCal impeller at the 220mm size that will sit inside the casing, draw greater air and not be much louder than my current portable unit.
I’ve started looking at the power requirements and put thought to bothering an electrician.
Design merits and flaws
I thought about my ventilation system and have been looking at fans. I’ve done research on fans. I’ve learned more than I care to about the science behind how fans work and what makes them work. The problem is that I am still learning and gaining no benefit from the insight. I thinm George Carlin once said “I do not possess a degree in engineering nor am I mechanically inclined”… I too am so blessed.
I thought, ‘I want a quiet fan for my airbrush system that will take up minimal space’; that wasn’t too unreasonable as an original assumption that it could be done. Here I am learning about impeller shapes and their effect on power efficiency and movement of air volume. I’m looking at how to control the unit, because simplicity can’t be achieved when you let an engineer in the room (don’t look at me like that; he was carrying donuts).
I wish I could just scrawl out notes by hand here for that satisfaction of having created something with all the information. It might be easier on the mind of you, the reader, if I didn’t though as editing would be so much more difficult.
I guess there might be some things to list where I needed to put more thought.
- directing airflow
- fan mounting
- fan controls/power
- access to components
Back to the drawing board as I put more thought into the fan. The case might as well be chucked as I have overlooked basic issues. The first is mounting the fan. I had assumed that I could just mount a fan to the back and have a housing direct the air out of the unit. I was partially right here. There would need to be some way of directing air in.
Any air handler unit has air coming in through a filtration medium and then moves it away; that’s a simple enough premise. I had seen what goes on in the basic model of portable airbrush units and it seemed straightforward. The problem started when I changed the direction of airflow. The basic fan is straight from the front to the back. The fans I’ve found that are quiet direct the air at a 90° angle to the intake. This means I need to build something around the fan to have the air exit where I want it; it needs to be some sort of thin divider. This creates a problem for accessing parts inside the case when the front half is closed off from the rear portion.
Problems part … well, the next one… how to get to the insides. As I thought that there would be easy access to the guts from the get go I didn’t throw in any doors for the housing. How wrong I am as I keep putting in more thought. There should be some sort of access door or at least a better means of shutting out the ventilated air. I see that there could be more work done in the build that I cannot address at present without the use of a blowtorch or redesigning from the ground up on a CNC machine before bending parts.
My next issue it seems would also be related to others as I designed the case and didn’t have a clue as to what the electronics inside might be nor the size shape of the controls. I do regret the lack of knowledge but now that I have it I can say that the case is lost… or at least I hope it isn’t. All in all I think that having this as a slow burn build is helpful as I try to figure this out. I will have the quietest fan possible with the least amount of problems (only after hammering out the issues) that you too can recreate with the least of issues as I trudge forth into the fray of designing woes.
A little boxed in at the moment
Life throws curveballs and has unexpected surprises. Today is not really an exception. I was told Wednesday that Friday would be my last day of work for my present employment. This isn’t too much of a surprise for being a temporary laborer but a pain in the butt after nearly six months. Today, however, I was given the chance to work on my project. I got all the build done from the metal shop with minimal assistance. I started off with getting the plans to the guy who runs the CAD operation to put in the coordinates for the laser cutter to work with. After this there was quite a bit of using hand brakes to fold the angles before the spot welding to secure metal in place. The final touch was getting a vent port on, spot welding it and then sealing it with polyurethane.
There’s more to come that may include getting another piece of metal inside as an attachment arm for when I have the fan on hand. Assembling the electrical connections will be easy enough after a little research. After that I’ll build the hood and sides for collection and then spray paint it all for uniformity.
This is coming along pretty well I’d say even iff a little off kilter and probably in need of some feet for better balance.
Turning to those with experience for help
Working in HVAC has definitely brought more info to me than I would have been privy to without other people with experience related to what I’m planning. So, what the spray booth really boils down to what is known as a filter rack and have a spring loaded door for easy filter replacement. This particular fitting is pretty easy to build as I’m told by the more senior guys in the shop. From what I see it seems to be the case. I just need to figure out what fan I’m going to buy and then install inside. Looking at the specs that are provided on the fan for the BV300SD there are plenty of units to look at and consider with care given to the relative noise and approximate size.
Something else I’ve thought about is the filters used in videos I’ve watched. Realistically for me the replacement of these filters would be a pain as they look to be a general poly fiber material, the likes of which you’d use in a fish tank, with “bird wire” mesh covering them. I’ll be ditching the poly fiber idea. I’ve seen the ventilation of pharmaceutical plants and office spaces during my security work in the past and I know what kind of pain it might be to make it economical on the small scale. I’m going to be using pleated filters used for home heating. So far the MERV 11 rating catches all the overspray from my airbrush and I’ll stick with that. The size will depend on the fan motor and rack area. Premade filters will be a great boon as I’ve taken other filters and cut them to fit my small portable Chinese made spray booth.
Now I need to get info on the ducting as I think a hose fitting and a hole for the switch on the side will also need to be planned for in future for plotting on the plasma cutter. The other fittings like a handle and rubber feet I can probably add with self tapping screws. This might be a good time to learn about electrical wiring as I need to have it run on something other that an orkish Gestalt field.
More than just blowing one's nose
I’ve been in the market for a new spraybooth to replace the one I have currently. I’ve come across repeated reviews of the Benchvent BV300S-D Spray Booth as being top of the line for moving air. I’ve seen other units but they just doesn’t seem to compare for air volume. The real downside is the cost which I hope to avoid by making this at work.
Presently I’m in the good position of working at a sheet metal shop that does quite a bit of work with large scale ventilation systems. I’m still not on entirely as I’m only in the probationary period before starting an apprenticeship program but I’ve thought that this would be a damn good project to learn the skills required for the full time operations. I think that it might also work well to show motivation for the work being done. If I’m willing to learn and put in the time it can’t hurt my chances.
All in all I hope to build a unit for airbrushing that I don’t need to pay an arm and a leg for. Hell, I might even get some powder coating done to make it all fancy and professional looking. Here goes nothing.