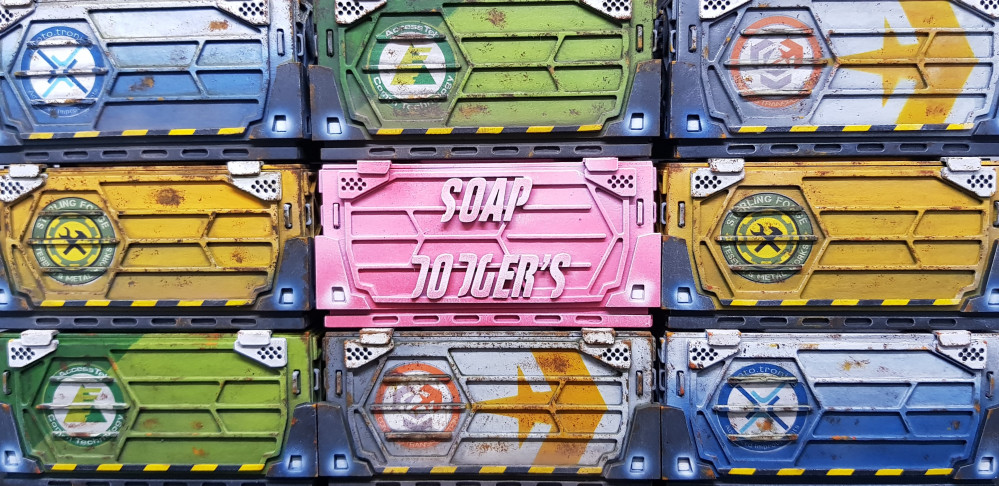
Infinity Terrain
Revenge of the staircase.
Long time no progress. I took a few weeks off from this. I burnt out on this project so moved on and messed around. Now I am back cutting and printing again.
Usually my burn outs happen when something doesn’t go right. This was no exception.
I cut out 100 parts it takes to build this staircase. this in itself is not slow or difficult. It was good to see I managed to laser cut the fibreglass mesh. I rush to assembly on my old GW brush that would make the core.
Problem was I was using superglue and going this (started in the light) in the dark. It was ok not great until about 2/3 of the way up. Then I glued a stair in bent and then proceeded to put the rest on and only noticed when I was done. I then broke it numerous times trying to fix it and in the end it was not very accurate and not up to my own standards.
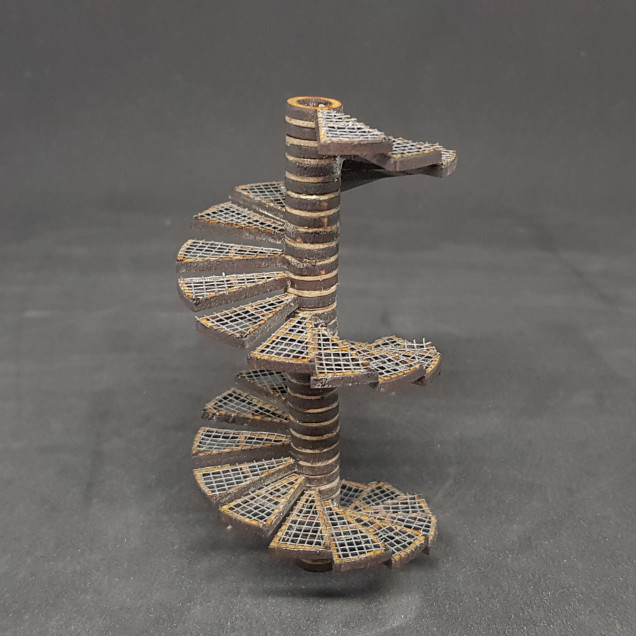
So I did learn from my mistakes. I learned to play more and have more fun. I have played 4 games of infinity in-between then and now which is more than I have played all year. I am now no longer using the starter rules and am having to copy with the loads of special rules. I did miss not having the landing pad around to use to play on so I guess I had to get back to it and that meant dealing with the staircase.
I started with the banister one of the issues was even though I was kind of accurate with the rotation it wasn’t great. So last night while playing infinity I got the print on the go. This is the largest print I think I have done so far on the photon and for such a small part.
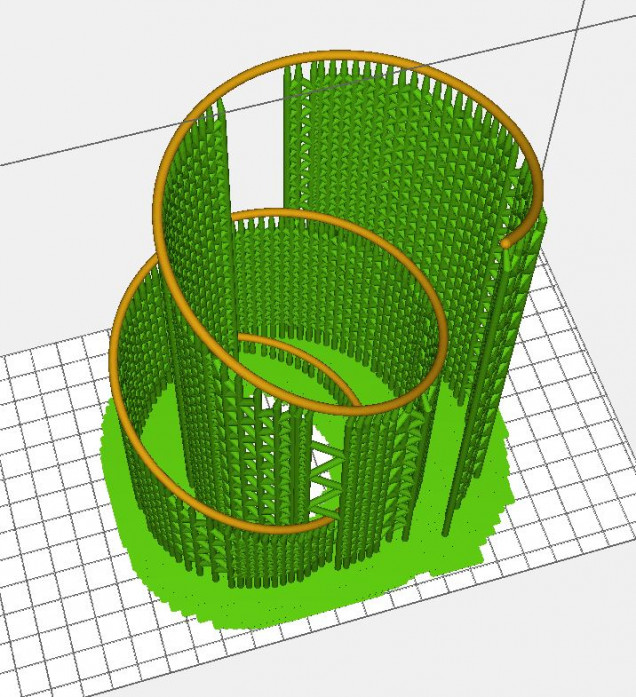
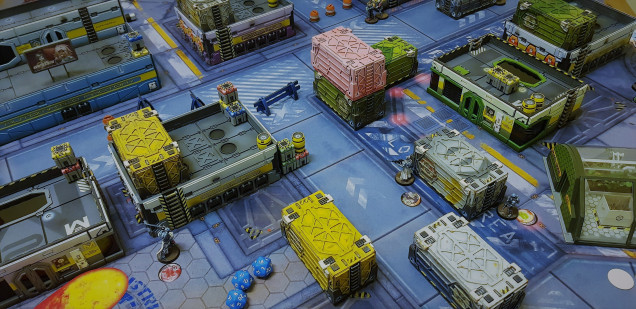
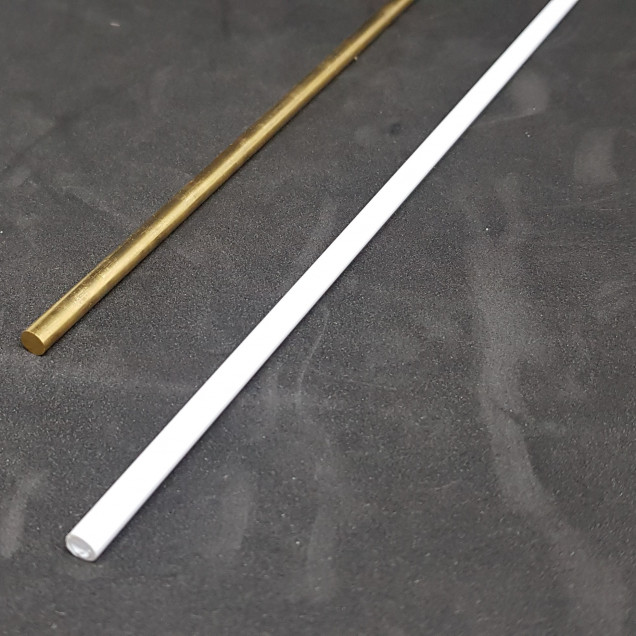
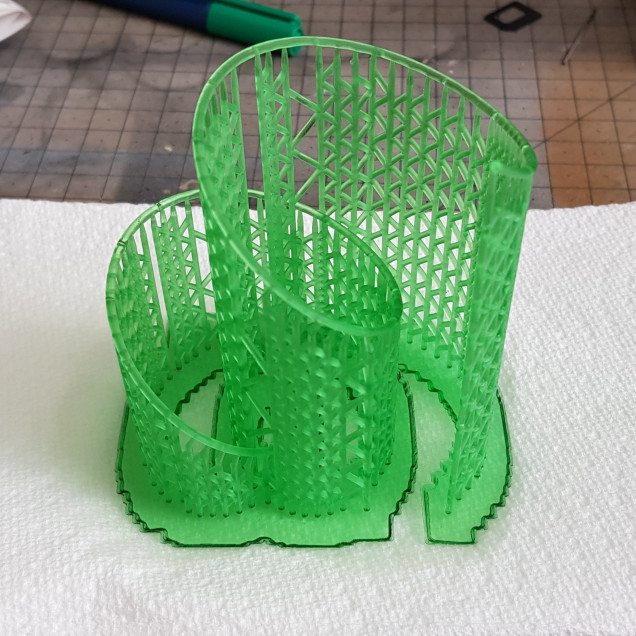
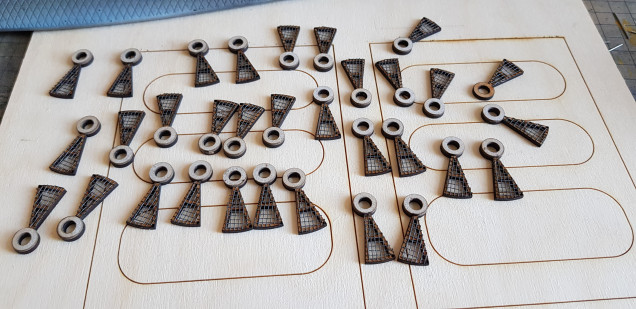
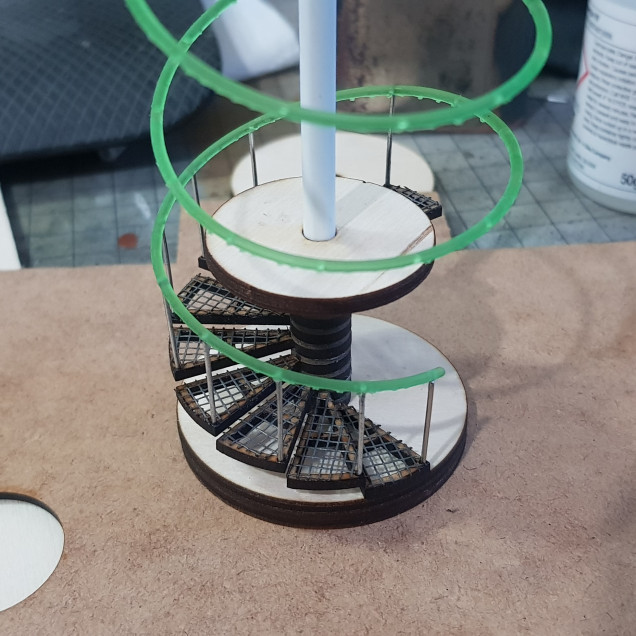
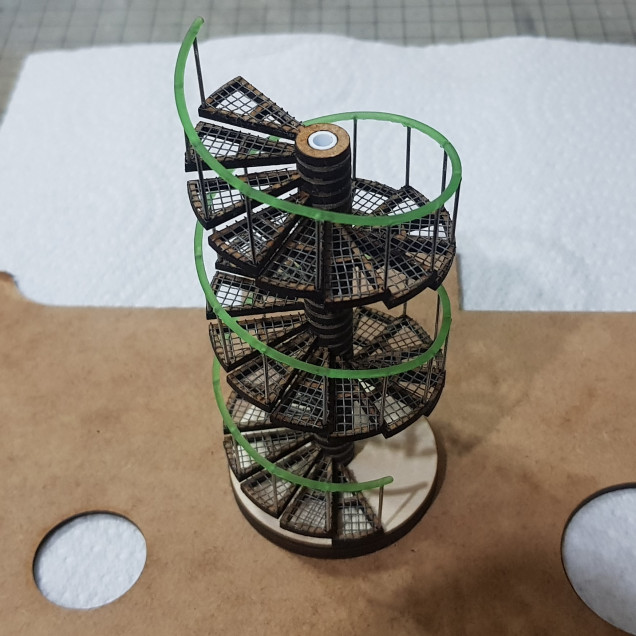
I have the 3D printed parts for the second platform printing just now as I type. I have already laser cut the top and bottom of the platform. I will be doing this over the next couple of days and then I will be ready to start assembly and then painting again.
I don’t think I have learned my lesson for making and designing things that are very complicated. Cant wait to get this finished though.
More to come.
Leave a Reply